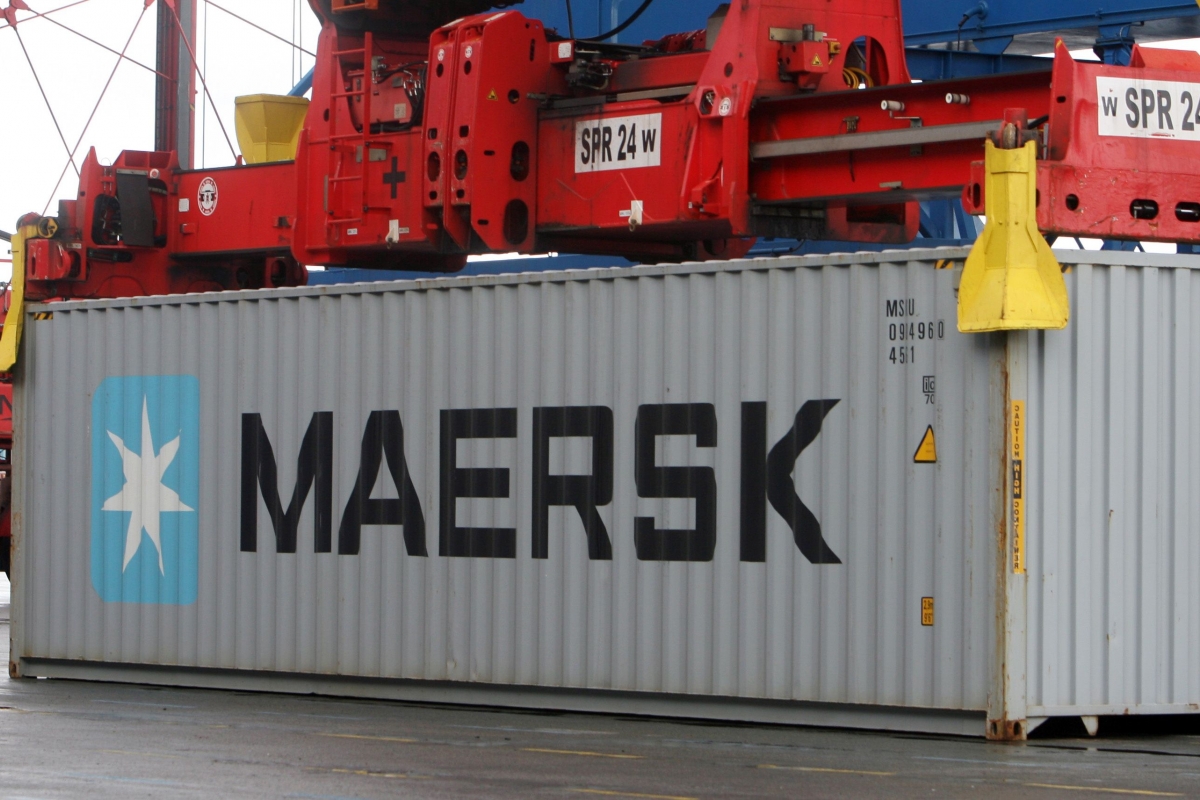
Note: Maersk presented the following paper to in its meeting with Globalization Monitor on 6 Apr 2009, together with "A Response to Globalization Monitor"
Browse to read: http://www.globalmon.org.hk/en/01news/04report-on-maersk/ap-moller-maer…;
This is not an exhaustive action list, but covering the key points. Where no other dates are noted, implementation will start now and be in place within the next few months. In the case of middle management review and training, implementation is expected to take longer, but will be initiated immediately.
Health & Safety
The international advisor and auditor on working environment, CRECEA, focused on the technical aspects of Health & Safety. Improved extraction of welding fumes CRECEA suggested improvements on extraction of welding fumes and acknowledged that an improved system under implementation since mid-2008 and to be completed by mid-2009 would adequately address the issue. Improved protection against noise Measurements confirmed an official report that noise levels were found to be high in some areas due to the nature of the work. New, improved hearing protection equipment has already been put into use. Going forward, management is working with shop floor employees and 3M to develop new protection equipment. Renewed efforts ensuring that employees use the protection equipment correctly will be made in cooperation with the MCID Labour Union H&S administration and communication
The assessment uncovered a clear need for improved communication and for a more efficient process to assist employees under medical supervision. A better process in general for employees who have a suspected occupational disease as well as those under medical supervision will be implemented. Each such employee will be assigned a personal case officer in HSE, who will help them through the process and expedite matters at the hospital and in MCID administration. Case officers will regularly, and with relatively short intervals, communicate with the individuals to keep them informed of the current status. The overall conclusion of the audit conducted by CRECEA found that MCID was above average Chinese level regarding Health and Safety. The audit team observed many positive achievements, but also highlighted areas that could be improved as noted above.
Labour Rights / Human Rights
China team from UK based consultancy, Impatt Ltd, specialised in labour standards and factory assessments, focused on the shop floor employees and their views of working at MCID. Impatt also conducted a thorough review of the Employee Handbook against Chinese Labour Law and ILO Conventions. Better shop floor employee representation in Labour Union The low number of shop floor employees in the Labour Union committee left shop floor employees with a feeling of not being properly represented. Although the election was conducted in a transparent and democratic way, the Labour Union itself as well as management sees this as unfortunate and the Labour Union has following the audit drawn up plans to encourage representatives to elect more shop floor employees in upcoming by-elections and by taking an initiative to create a sub committee solely manned with shop floor employees. Reviewed Employee handbook The employee handbook has been reviewed based on Chinese law and ILO conventions and an updated handbook is ready for implementation as soon as it has been approved by the Labour Union representatives, expected latest May. Simplified salary structure A new and simplified salary structure has been under implementation in stages since June 2008. The implementation will be completed in connection with the annual April salary review in line with the overall A.P. Moller-Maersk organization.
Culture and daily life
The assessment indicated mistrust by shop floor workers towards middle management causing a feeling of a poor middle management attitude and of unsatisfactory promotional opportunities. Improved management skills The assessment only having focused on the shop floor employees a subsequent assessment will focus on middle management to complete the picture. Meanwhile, steps are being taken to improve management skills and to implement personal evaluations of each middle manager. New processes to prevent corruption Allegations of corruption were heard but no firm or actionable evidence put in front of management. Nevertheless, corruption is naturally not accepted and MCID deals firmly and impartially with corruption, theft, illegalities etc. when identified. New processes have already been put in place and more will follow to reduce the risk for corruption. Examples of those implemented are elimination of management layers and a revised approval procedure aimed at ensuring a fair promotion process. Improving communication between employees and management In general, management is looking into ways of expanding vertical communication channels. Various models will be tested to see what works the best.
This is a long term effort. Review of dismissals Review of all dismissals at MCID in 2008-2009. Dismissals will be reviewed in line with the recently amended handbook and compensation, if any, will be handled accordingly. Furthermore, should a case review leave any doubt about the fairness of the dismissal, we will give the dismissed person the benefit of the doubt and compensate accordingly. The overall survey concluded that 86% of shop floor employees were content or outright satisfied with the factory environment. The improvements made over the last year, were appreciated by employees. This will however not prevent management from implemented the actions stated above to further improve the working environment and daily life at the factory.
Follow up A re-audit will be undertaken before end 2009 to monitor progress of implementation.